SOMMAIRE
- L’évolution du paysage MES vers des solutions évolutives
- L’adaptabilité des solutions MES selon les différents écosystèmes et niveaux de maturité digitale des industries
- Les défis de la transformation digitale : où s’arrête la portée du MES ?
La transformation numérique des industries est un enjeu majeur pour la compétitivité des entreprises. Au cœur de cette révolution, les systèmes d’exécution de la production (MES – Manufacturing Execution System) jouent un rôle central. Dans cette tribune, Ludovic Verzier, Directeur Commercial chez Premier Tech Digital, partage son expérience et sa vision des défis actuels et futurs de la digitalisation industrielle.
Pas le temps de lire ? Voici le résumé de la tribune !
Dans cette tribune d’expert, Ludovic Verzier, Directeur Commercial chez Premier Tech Digital, explore la digitalisation industrielle à travers l’implémentation des systèmes d’exécution de la production (MES). Cette tribune met en avant l’évolution du marché des MES vers des solutions plus flexibles, intégrant à la fois standardisation et personnalisation pour répondre aux besoins spécifiques des entreprises. Dans ce contexte, l’approche agile est privilégiée pour éviter les projets lourds et inefficaces, en favorisant des cycles courts de développement. L’intégration des MES dans l’écosystème IT/OT existant est importante pour optimiser les flux d’information, en évitant les redondances avec les ERP. M. Verzier souligne également les défis liés à l’adoption des technologies émergentes comme l’IoT et l’IA, et l’importance de l’évolution des compétences au sein des entreprises. Enfin, il insiste sur une approche pragmatique de l’industrie 4.0, où le MES devient une plateforme centrale d’innovation pour l’usine connectée et intelligente dans l’optimisation des processus et la prise de décision.
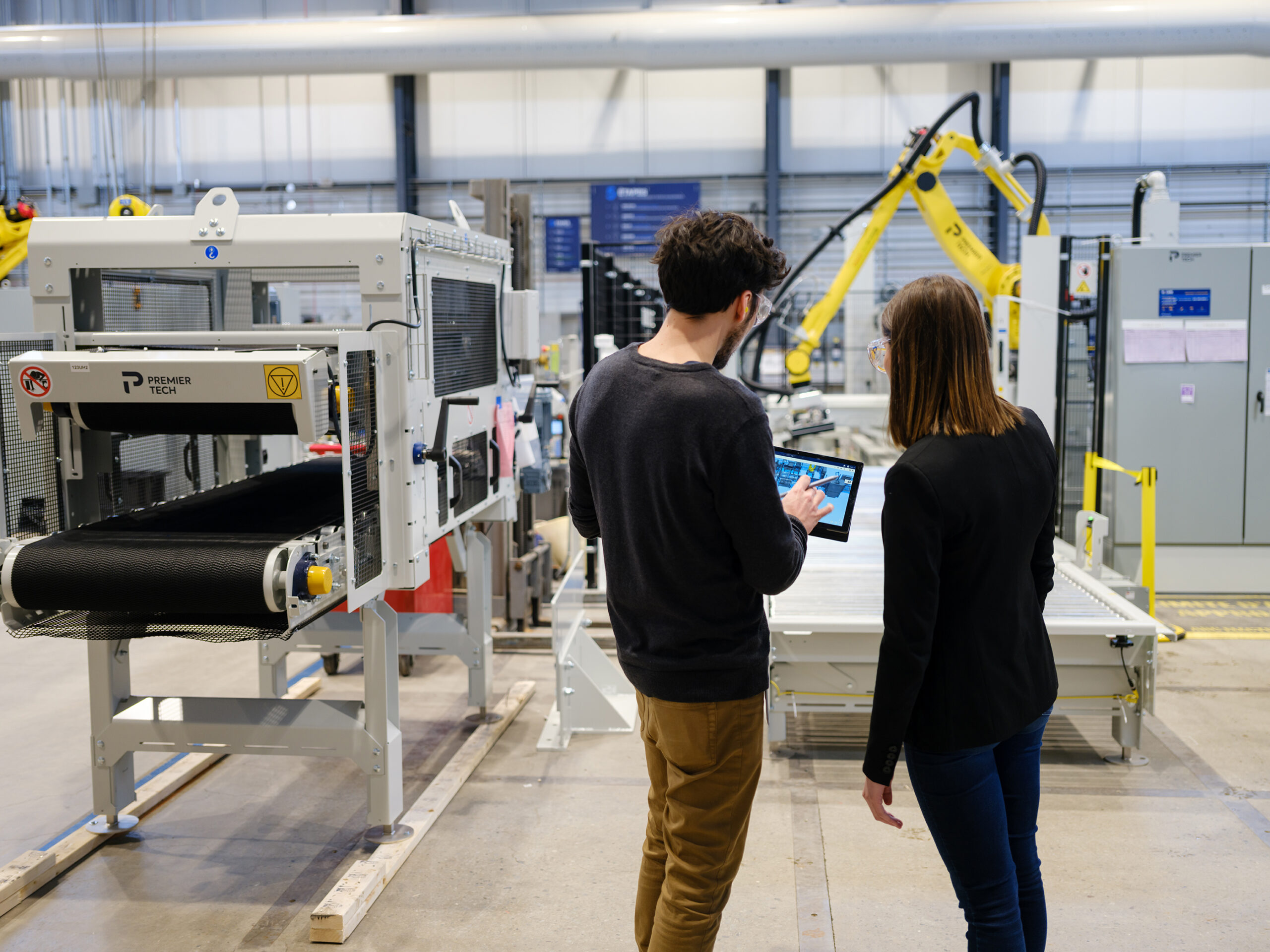
L’évolution du paysage MES vers des solutions évolutives
Le marché des solutions MES a considérablement évolué ces dernières années. Nous sommes passés d’un modèle où dominaient les éditeurs de logiciels propriétaires d’un côté et les intégrateurs purs de l’autre, à un écosystème plus hybride et flexible. Cette évolution répond à un besoin croissant de solutions adaptables, capables de s’ajuster aux spécificités de chaque industrie tout en bénéficiant des avantages des systèmes standardisés.
- Les enjeux de la personnalisation
Dans ce contexte, l’un des défis majeurs dans l’implémentation d’un MES est de trouver le juste équilibre entre standardisation et personnalisation. Chaque client considère ses processus comme uniques, nécessitant des adaptations spécifiques. Cependant, l’expérience montre qu’une grande partie des besoins en MES peuvent être couverts par des fonctionnalités standard.
La clé réside alors dans une analyse approfondie des besoins en amont du projet, la « phase de découverte ». Cette étape majeure permet de définir précisément les besoins du client, d’élaborer des maquettes d’interface utilisateur (UI/UX) et de planifier une feuille de route de digitalisation adaptée.
- L’importance de l’agilité dans les projets MES
Les projets MES traditionnels ont souvent souffert de cycles de développement trop longs, aboutissant parfois à des solutions surdimensionnées ou inadaptées aux besoins réels des utilisateurs. Pour pallier ce problème, il est préconisé une approche par cycles courts pour garantir de livrer rapidement des modules fonctionnels, de les tester en conditions réelles et de les faire évoluer en fonction des retours d’expérience.
Cette approche agile est particulièrement pertinente pour les entreprises qui débutent leur transformation numérique. Elle permet d’accompagner progressivement le client dans sa montée en maturité digitale, tout en évitant les écueils des projets pharaoniques qui peinent à aboutir.
- L’intégration du MES dans l’écosystème IT/OT
Un autre enjeu majeur des projets MES est leur intégration dans l’écosystème informatique et opérationnel existant. Le MES se positionne comme une couche intermédiaire entre l’ERP (Enterprise Resource Planning) et les équipements de production. Il est important de bien définir les périmètres fonctionnels de chaque système pour éviter les redondances et optimiser les flux d’information.
Dans de nombreux cas, les entreprises ont tendance à surcharger leur ERP avec des fonctionnalités qui relèvent du MES. Il est important de comprendre que l’ERP est un outil de gestion en temps différé, alors que le MES opère en temps réel au plus près de la production. Cette distinction est fondamentale pour concevoir une architecture IT/OT cohérente et performante.
“Le but de la phase de découverte est de partir du besoin du client et de définir une roadmap de digitalisation. Pour garantir l’atteignabilité de cette roadmap, on découpe le besoin client pour faire des cycles de 4 mois de sorte que sur chaque cycle, il ait un module avec un certain nombre de fonctionnalités qui seront mises en place, implémentées et sur lesquelles il va commencer à vivre. L’objectif est d’avoir un produit qui évolue et qui suive la feuille de route pour répondre à ses besoins définis en amont.”
Ludovic Verzier, Directeur Commercial chez Premier Tech Digital
L’adaptabilité des solutions MES selon les différents écosystèmes et niveaux de maturité digitale des industries
La mise en œuvre d’un MES présente des enjeux différents selon la taille et la maturité digitale des entreprises. On peut distinguer deux cas de figure principaux :
- Les petites entreprises peu digitalisées
Ces entreprises, souvent équipées uniquement d’un ERP, font face à plusieurs défis :
- La compréhension du rôle du MES : Il est important de comprendre que l’ERP, conçu pour une gestion en temps différé, n’est pas adapté pour gérer les opérations en temps réel de l’atelier.
- L’absence d’infrastructure IT dédiée à la production : La mise en place d’un MES nécessite souvent de créer une infrastructure réseau spécifique pour l’atelier.
- La résistance au changement : L’introduction d’un MES implique une modification importante des habitudes de travail, notamment le passage du papier au numérique.
Malgré ces défis, ces entreprises présentent l’avantage de partir d’une « feuille blanche » en termes de digitalisation de la production, ce qui peut faciliter l’adoption d’une solution MES moderne et intégrée.
- Les entreprises matures digitalement
Pour les entreprises déjà équipées de solutions digitales, les motivations pour adopter ou faire évoluer un MES sont souvent liées à des besoins spécifiques :
- La connectivité : Le besoin de collecter automatiquement des données des équipements de production, que ce soit pour mesurer la performance, la qualité ou simplement pour le comptage de pièces.
- L’intégration de nouvelles fonctionnalités : Par exemple, la gestion de l’énergie, qui bien que non directement liée au MES, s’intègre dans une stratégie de digitalisation globale de l’usine.
- L’agrégation et l’analyse avancée des données : Les plateformes MES modernes permettent de corréler différentes sources de données (production, maintenance, etc.) pour une analyse plus fine et une prise de décision plus éclairée.
Ces entreprises sont généralement plus exigeantes en termes de fonctionnalités et d’intégration, ce qui peut complexifier le projet MES.
“Sur les clients que j’aborde aujourd’hui, généralement les petites structures n’ont pas forcément d’outils digitaux en-dehors d’un ERP qui descend sur les lignes de production. L’enjeu est donc de définir quels sont les apports et les limites de l’ERP, et comment le système de MES peut venir compléter ce fonctionnement, avec notamment l’apport de données en temps réel et tous les avantages que ça représente.”
Ludovic Verzier, Directeur Commercial chez Premier Tech Digital
Les défis de la transformation digitale : où s’arrête la portée du MES ?
La transformation digitale des industries ne se résume pas à l’implémentation de nouvelles technologies. Elle implique également une évolution des processus et des compétences.
- L’évolution des compétences
La mise en place et l’exploitation d’un MES moderne nécessitent de nouvelles compétences au sein des entreprises industrielles. Au-delà des connaissances techniques sur les processus de production, il devient essentiel de maîtriser les concepts de l’informatique industrielle, de l’analyse de données et de la gestion de projet agile.
Cette évolution des compétences représente un défi pour de nombreuses entreprises, en particulier les PME qui ne disposent pas toujours des ressources nécessaires en interne. Le recours à des partenaires externes, capables d’apporter expertise et accompagnement, devient alors nécessaire pour mener à bien les projets de digitalisation.
- L’apport des technologies émergentes
L’Internet des Objets (IoT) et l’Intelligence Artificielle (IA) sont souvent présentés comme des technologies révolutionnaires pour l’industrie. Si leur potentiel est indéniable, leur adoption dans le monde industriel suit une courbe de maturité plus lente que dans d’autres secteurs.
L’IoT, par exemple, offre de nouvelles possibilités pour la collecte de données, avec des capteurs plus faciles à déployer et moins coûteux. Cependant, il est important de noter que la collecte de données industrielles n’est pas nouvelle en soi. Ce qui change, c’est la facilité d’accès à ces données et les capacités accrues de traitement et d’analyse.
Quant à l’IA, si elle suscite un intérêt certain, son adoption concrète dans les projets MES reste encore limitée. Les industriels sont curieux de ces technologies, mais le passage de l’intérêt à l’investissement reste un défi. Il est important de démontrer la valeur ajoutée concrète de ces technologies pour justifier leur intégration dans les projets MES.
- Les nouvelles frontières du MES
Si le cœur de métier du MES reste la gestion de la production, ses frontières s’élargissent pour intégrer de nouvelles problématiques. La gestion de l’énergie en est un exemple frappant. De plus en plus d’entreprises cherchent à intégrer des fonctionnalités de suivi et d’optimisation énergétique dans leur MES, souvent dans le cadre de démarches de certification comme l’ISO 50001.
Cette évolution illustre la tendance à l’agrégation des données au sein de plateformes digitales globales. L’enjeu n’est plus seulement de collecter des données, mais de les mettre en corrélation pour en extraire des informations pertinentes. Par exemple, la capacité à croiser des données de consommation énergétique avec des événements de production ou des facteurs externes ouvre de nouvelles perspectives d’optimisation.
- Vers une industrie 4.0 réaliste
Le concept d’Industrie 4.0, largement médiatisé ces dernières années, a parfois créé des attentes démesurées. Il est important d’adopter une approche pragmatique de la digitalisation industrielle, en se concentrant sur des objectifs concrets et atteignables plutôt que sur des visions futuristes.
Le MES joue un rôle central dans cette approche réaliste de l’Industrie 4.0. En fournissant une vision en temps réel de la production, en optimisant les processus et en facilitant la prise de décision, il constitue une base solide pour construire l’usine du futur. Les technologies plus avancées comme l’IA ou la réalité augmentée pourront venir se greffer sur cette base, au fur et à mesure de leur maturation et de la démonstration de leur valeur ajoutée.
“Une question qu’on se pose souvent, c’est est-ce qu’une plateforme de digitalisation doit nécessairement s’appeler un MES ? Et dans quelle mesure ce qu’apporte un MES aujourd’hui sera la même chose dans dix ans ? Car un MES répond à plusieurs besoins : gestion de production, gestion de la qualité, gestion de la digitalisation du processus de suivi de production, etc. Et les frontières sont de plus en plus compliquées à définir entre un ERP, un WMS, une GMAO, un LIMS et le MES. Donc au final, est-ce le nom MES et ce qu’il représente serait amené à évoluer ?”
Ludovic Verzier, Directeur Commercial chez Premier Tech Digital
La digitalisation industrielle, et en particulier l’implémentation de systèmes MES, est un voyage plus qu’une destination. Elle nécessite une approche équilibrée, combinant standardisation et personnalisation, agilité et rigueur, innovation technologique et pragmatisme opérationnel.
Les entreprises qui réussiront leur transformation digitale seront celles qui sauront naviguer entre ces différents impératifs, en s’appuyant sur des partenaires capables de les accompagner dans la durée, tels que Premier Tech Digital. Le MES de demain ne sera pas seulement un outil de gestion de la production, mais une véritable plateforme d’innovation, au cœur de l’usine connectée et intelligente.
Dans ce contexte en constante évolution, il est fondamental pour les industriels de rester à l’écoute des nouvelles tendances tout en gardant un œil critique sur leur pertinence réelle. La clé du succès réside dans la capacité à identifier les technologies et les approches qui apporteront une valeur ajoutée concrète à l’entreprise, plutôt que de céder aux effets de mode.
Enfin, n’oublions pas que la technologie n’est qu’un moyen au service d’une fin. L’objectif de la digitalisation industrielle reste l’amélioration de la performance, de la qualité et de la flexibilité des processus de production. C’est en gardant cet objectif à l’esprit que les entreprises pourront tirer pleinement parti des opportunités offertes par le MES et les technologies associées, pour construire l’industrie de demain.
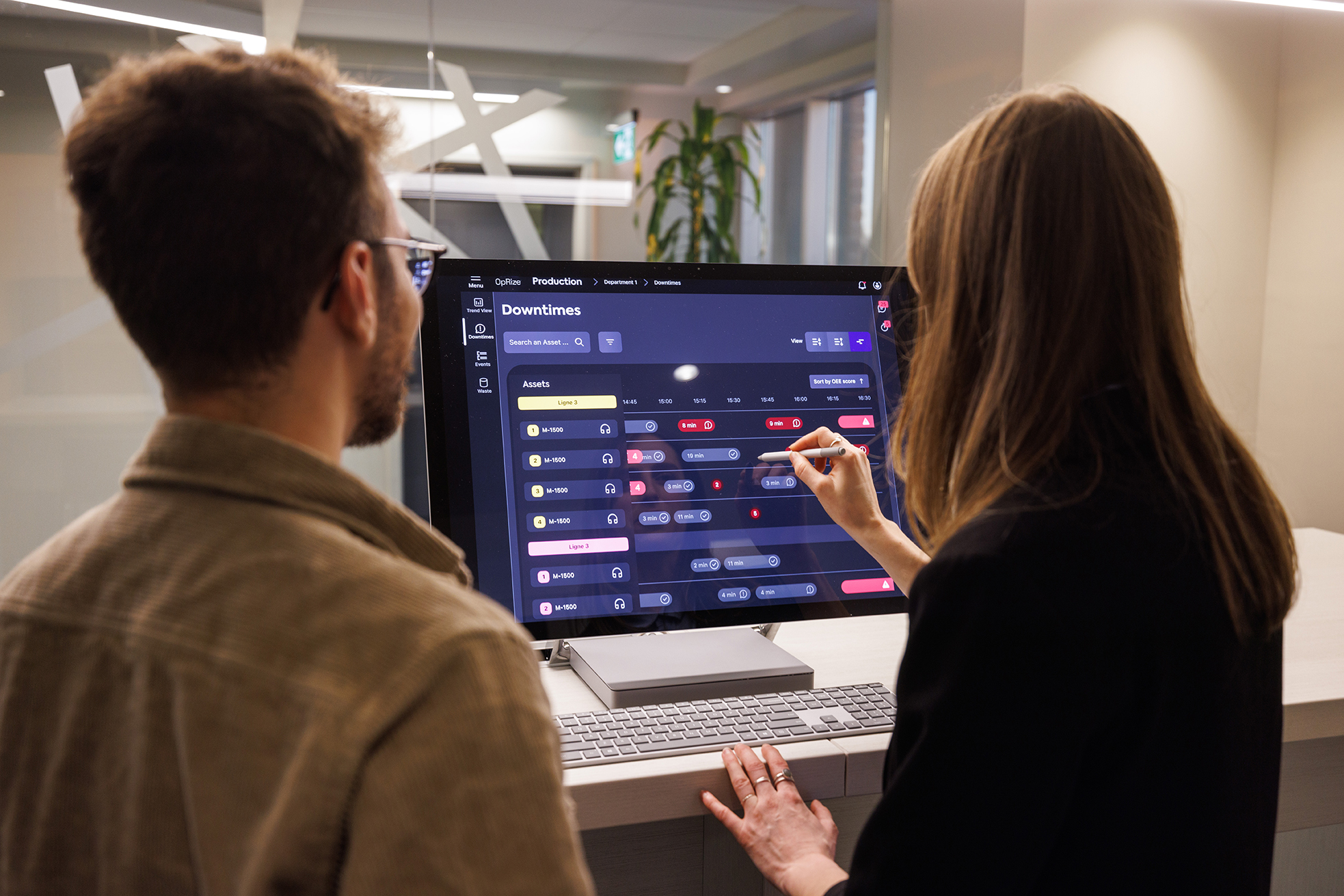
Cette tribune a été proposé par Premier Tech Digital.
Cet article vous a plu ? Partagez-le sur Linkedin :