SOMMAIRE
- La complémentarité entre PLM et MES
- L’implémentation du MES : un défi technique et humain
- La définition de stratégies pour une implémentation réussie
- Des opportunités prometteuses d’une interaction plus forte entre PLM et MES
Dans le monde industriel en constante évolution, les entreprises cherchent continuellement à optimiser leurs processus et à améliorer leur efficacité opérationnelle. Cette quête d’excellence a conduit à l’émergence et à l’adoption de systèmes informatiques sophistiqués, dont deux piliers majeurs sont le PLM (Product Lifecycle Management) et le MES (Manufacturing Execution System).
Dans cette tribune, Christian Genez, Senior Project Manager chez INENSIA, explique comment ces deux systèmes, bien que distincts dans leurs fonctions primaires, sont de plus en plus interconnectés, offrant une vision globale et intégrée de la chaîne de valeur industrielle.
Pas le temps de lire ? Voici le résumé de la tribune !
L’intégration du PLM et du MES représente une étape importante dans la transformation digitale des entreprises industrielles. Elle offre des opportunités significatives d’amélioration de la performance et de l’agilité opérationnelle. Cependant, la réussite de ces projets repose en grande partie sur une conduite du changement efficace, prenant en compte les aspects humains, organisationnels et culturels de la transformation.
La définition d’un modèle de base commun, l’adaptation aux spécificités locales, la formation et l’accompagnement des utilisateurs, la gestion des résistances au changement, et la prise en compte des différences culturelles sont autant d’éléments clés de cette conduite du changement.
Dans cette tribune, Christian Genez, Senior Project Manager chez INENSIA, retrace les opportunités et les défis spécifiques liés à l’implémentation du MES, notamment sa criticité opérationnelle et son intégration centrale dans le paysage applicatif, et l’importance d’être intégré dans une approche structurée et méthodique de la conduite du changement.
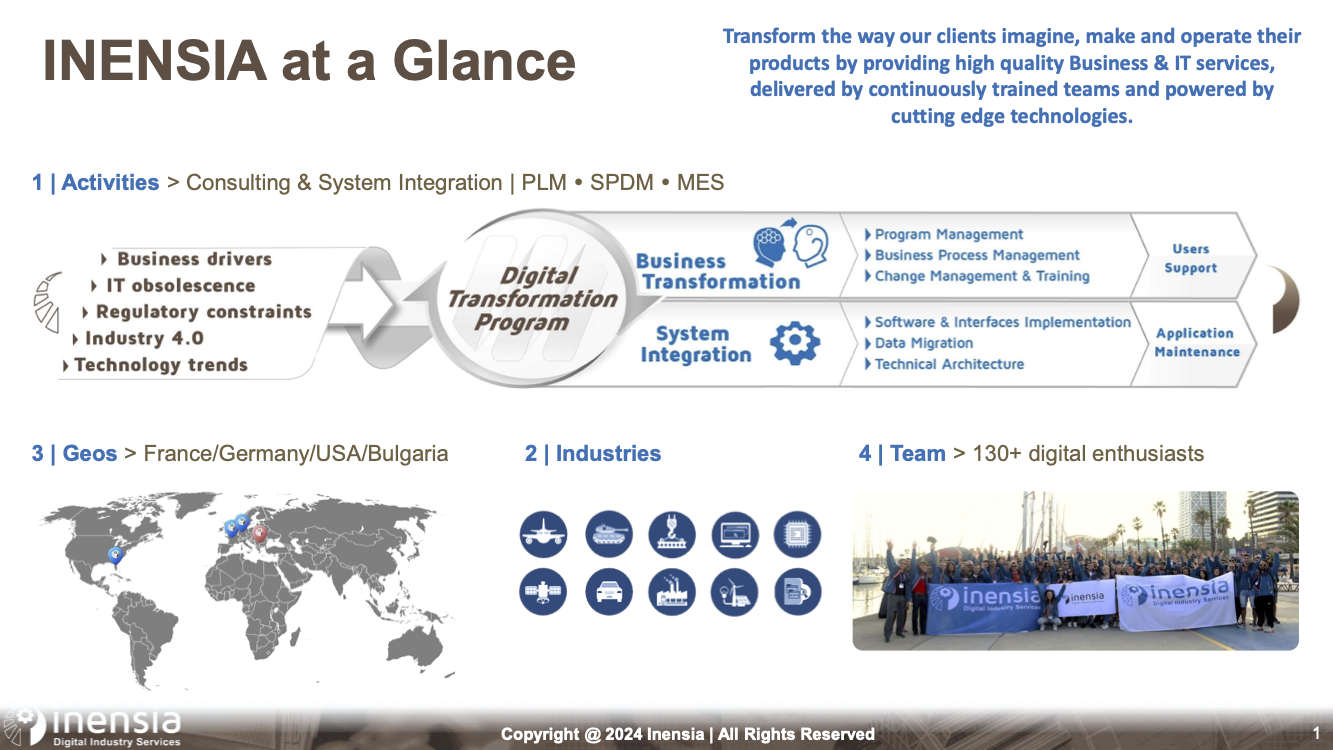
La complémentarité entre PLM et MES
Le PLM, historiquement ancré dans le domaine de l’ingénierie, se concentre sur la gestion du cycle de vie des produits, de leur conception initiale à leur fin de vie. Il englobe la gestion des données produits, la collaboration entre équipes d’ingénierie, et la traçabilité des modifications tout au long du cycle de développement. Le MES, quant à lui, se positionne au cœur de l’atelier de production, orchestrant les opérations quotidiennes, de la planification à l’exécution des ordres de fabrication.
La complémentarité entre ces deux systèmes réside dans leur capacité à créer un continuum informationnel entre la conception et la production. Le PLM fournit au MES les données de base des produits, les nomenclatures et les gammes de fabrication. En retour, le MES alimente le PLM avec des données réelles de production, permettant ainsi d’affiner les conceptions futures et d’optimiser les processus de fabrication.
Cette synergie entre PLM et MES s’inscrit dans une vision plus large de l’industrie 4.0, où la continuité numérique est au cœur des préoccupations. L’intégration de ces systèmes favorise une réactivité plus forte face aux changements de conception, une meilleure gestion de la qualité, et une traçabilité renforcée tout au long du cycle de vie du produit.
“La continuité du PLM en le couplant à une solution MES apporte plusieurs bénéfices aux clients, notamment l’accès à des données vraies, en temps réel, et un paysage applicatif plus couvert, voire plus homogène selon les spécificités des clients.”
Christian Genez, Senior Project Manager chez INENSIA
L’implémentation du MES : un défi technique et humain
L’introduction d’un MES dans un environnement industriel représente un changement majeur, tant sur le plan technique que sur le plan organisationnel. Contrairement au PLM, qui s’adresse principalement à des équipes d’ingénierie déjà familiarisées avec les outils informatiques, le MES touche directement le cœur de l’atelier, impliquant des opérateurs parfois peu habitués aux interfaces numériques.
- Défis techniques
Sur le plan technique, l’implémentation d’un MES nécessite une intégration fine avec les systèmes existants, notamment l’ERP (Enterprise Resource Planning) de l’entreprise. Cette intégration doit assurer un flux d’informations fluide et en temps réel entre les différents niveaux de l’organisation. La synchronisation des données entre l’ERP, le MES et les équipements de production est essentielle pour garantir la cohérence des informations et l’efficacité des opérations.
Un autre défi technique réside dans la modélisation des processus de production au sein du MES. Cette modélisation doit être suffisamment flexible pour s’adapter aux spécificités de chaque site de production tout en maintenant une cohérence globale à l’échelle de l’entreprise. La notion de « core model » illustre cette problématique : définir un modèle de base commun à tous les sites, tout en prévoyant des possibilités d’adaptation locale.
- Défis humains et organisationnels
L’aspect humain de l’implémentation d’un MES est tout aussi important que l’aspect technique, sinon plus. La conduite du changement joue un rôle central dans la réussite du projet et implique plusieurs dimensions :
- Formation des utilisateurs :
Les opérateurs doivent être formés non seulement à l’utilisation de l’outil MES, mais aussi aux nouveaux processus de travail qu’il induit. Cette formation doit être adaptée aux différents profils d’utilisateurs et tenir compte des niveaux de maturité digitale variables au sein de l’organisation.
- Gestion des résistances au changement :
Il est fréquent de rencontrer des réticences face à l’introduction de nouvelles technologies dans l’atelier. Ces résistances peuvent être liées à la crainte de perdre en autonomie, à la peur de ne pas maîtriser l’outil, ou simplement à l’attachement aux méthodes de travail existantes. Une communication claire sur les bénéfices du MES et une implication des utilisateurs dès les phases amont du projet sont essentielles pour surmonter ces obstacles.
- Adaptation culturelle :
Dans le cas d’entreprises multinationales, l’implémentation d’un MES doit prendre en compte les différences culturelles entre les sites. Cela peut impliquer l’adaptation des interfaces utilisateurs aux langues locales, mais aussi la prise en compte des pratiques de travail spécifiques à chaque pays.
- Continuité opérationnelle :
Contrairement à d’autres systèmes comme le PLM, le MES est critique pour les opérations quotidiennes de l’atelier. Son déploiement doit donc être planifié avec une extrême précision pour éviter toute interruption de la production. Les utilisateurs doivent être opérationnels dès le premier jour de mise en production, ce qui ajoute une pression supplémentaire sur la phase de préparation et de formation.
« Il existe encore beaucoup d’ateliers où chaque matin, les opérateurs récupèrent une liasse papier pour savoir ce qu’ils vont devoir faire durant leur journée. Donc les embarquer dans le changement d’outil pour passer à l’informatique, ça peut ne pas être facile et on peut vite se retrouver avec des réactions comme : “Ça marchait bien avant. Pourquoi je m’embêterais avec un ordinateur ? »”
Christian Genez, Senior Project Manager chez INENSIA
La définition de stratégies pour une implémentation réussie
Face à ces défis, plusieurs stratégies peuvent être mises en œuvre pour maximiser les chances de succès d’un projet MES :
- Approche progressive
Une approche par étapes, commençant par un site pilote avant un déploiement plus large, peut s’avérer judicieuse. Cette méthode permet de tester le « core model » dans un environnement contrôlé, d’identifier les ajustements nécessaires, et de capitaliser sur les retours d’expérience pour les déploiements ultérieurs.
- Implication des utilisateurs finaux
L’implication des opérateurs et des responsables de production dès les phases de conception du MES est essentielle. Leur connaissance approfondie des processus de l’atelier est précieuse pour affiner le système et s’assurer de son adéquation avec les réalités du terrain.
- Flexibilité et adaptabilité
Bien qu’un « core model » soit nécessaire pour maintenir une cohérence globale, il est important de prévoir des mécanismes d’adaptation aux spécificités locales. Cette flexibilité peut se traduire par des modules configurables ou des extensions spécifiques à certains sites.
- Formation continue et support
La formation ne doit pas se limiter à la phase de déploiement initial. Un programme de formation continue et un support utilisateur réactif sont essentiels pour maintenir et améliorer les compétences des utilisateurs dans le temps.
- Gestion du multilinguisme
Pour les entreprises internationales, la gestion du multilinguisme est un aspect important. Cela implique non seulement la traduction des interfaces utilisateurs, mais aussi l’adaptation des processus et des documentations aux contextes locaux.
« Il y a eu toute une démarche de conduite du changement à haut niveau colossal pour la mise en place d’une solution MES chez un de nos clients. Ça a consisté, avant même que nous n’intervenions sur le déploiement de la solution, à revoir et à remodéliser l’ensemble des process de fabrication sur ces différents sites de production, en France et à l’étranger. Il y a eu une grosse conduite de changement, et on a été associé avec le client dès le début avec la définition du core model.”
Christian Genez, Senior Project Manager chez INENSIA
Des opportunités prometteuses d’une interaction plus forte entre PLM et MES
L’intégration croissante entre PLM et MES ouvre de nouvelles perspectives pour l’industrie, parmi lesquelles :
- Une continuité numérique renforcée : L’effacement progressif des frontières entre les différents systèmes d’information industriels devrait conduire à une meilleure fluidité des données tout au long du cycle de vie des produits.
- L’intégration de technologies émergentes : L’incorporation de technologies comme l’intelligence artificielle (IA), l’Internet des Objets (IoT) ou la réalité augmentée (AR) dans les systèmes MES pourrait apporter de nouvelles fonctionnalités et améliorer encore l’efficacité opérationnelle.
- Une approche plus agile de la production : La combinaison PLM-MES pourrait faciliter une approche plus agile de la production, avec une plus forte capacité à réagir rapidement aux changements de conception ou aux fluctuations de la demande.
- Une meilleure gestion de la qualité : L’intégration plus poussée entre la conception et la production devrait permettre une amélioration continue de la qualité, grâce à des boucles de rétroaction plus rapides et plus précises.
L’évolution du paysage applicatif industriel, marquée par l’intégration croissante entre PLM et MES, représente une opportunité majeure pour les entreprises de renforcer leur compétitivité. Cependant, la réussite de cette transformation numérique repose sur une approche équilibrée, prenant en compte à la fois les aspects techniques et humains du changement.
L’implémentation d’un MES, en particulier, nécessite une préparation minutieuse et une conduite du changement adaptée aux spécificités de l’environnement de production. Les entreprises qui réussiront à relever ce défi seront celles qui auront su combiner une vision stratégique claire, une approche technique solide, et une gestion humaine attentive.
Dans un contexte industriel en constante évolution, la capacité à intégrer harmonieusement ces systèmes d’information et à accompagner les équipes dans cette transformation deviendra un facteur clé de succès pour les industries du futur.
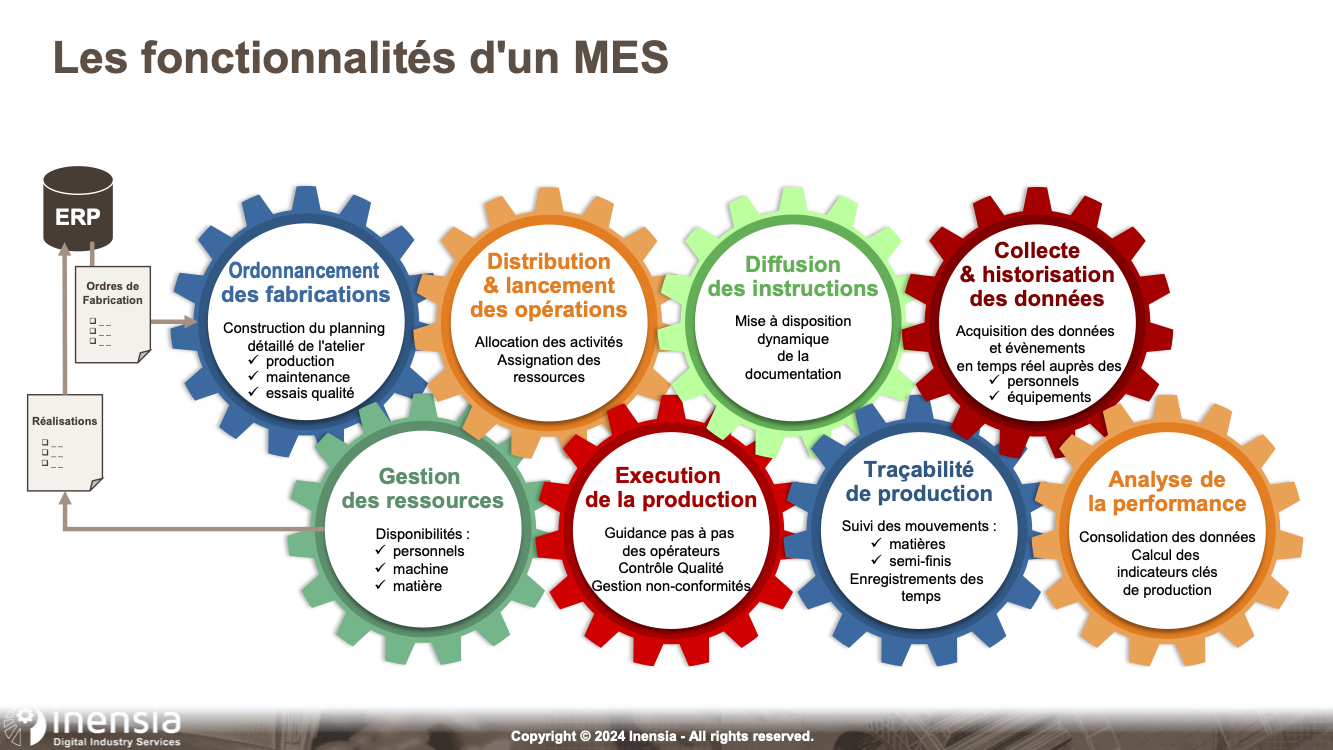
Cette tribune a été proposé par INENSIA.
Cet article vous a plu ? Partagez-le sur Linkedin :